Vulcanizing hydraulic presses are essential for producing durable, high-quality rubber products. In various industries, these machines mold, shape, and strengthen rubber materials by applying heat and pressure, thereby driving the vulcanization process. This process chemically converts natural rubber or related polymers into stronger, more elastic materials.
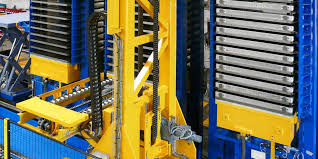
The Vulcanization Process
Charles Goodyear’s discovery of vulcanization in 1839 revolutionized rubber production. By heating rubber with sulfur, the process creates cross-links between polymer chains, which transforms rubber into a durable, elastic, and heat-resistant material. This transformation is crucial for producing tires, conveyor belts, hoses, gaskets, and seals that must endure extreme conditions.
The Role of Hydraulic Presses in Vulcanization
Vulcanizing hydraulic presses play a pivotal role in this process by delivering the necessary heat and pressure to start and sustain the chemical reaction. Thanks to precision engineering, these presses ensure uniform heat distribution and consistent pressure across the entire rubber piece. As a result, the process yields high-quality, homogenous products.
Key Components of Vulcanizing Hydraulic Presses:
The frame and structure provide the strength and stability needed to withstand the high pressures involved in vulcanization. Typically built from heavy-duty steel or iron, these components ensure durability and longevity.
The hydraulic system generates the required pressure to mold the rubber, utilizing a hydraulic pump, cylinders, and valves to apply pressure evenly across the mold. Consequently, this system ensures consistent product quality.
The heating system maintains the optimal temperature for vulcanization, typically using electrically heated platens to ensure consistent heat, which is vital for the integrity of the final product.
A control panel allows operators to set precise parameters for temperature, pressure, and curing time. This automation guarantees consistent product quality and reduces the likelihood of errors during production.
Molds determine the final shape of the vulcanized product. Typically customized for specific products, they are usually made of steel or aluminum to endure repeated heating and cooling cycles.
Types of Vulcanizing Hydraulic Presses
Vulcanizing hydraulic presses come in various configurations, each tailored to meet specific industrial needs. For example, compression molding presses mold rubber into complex shapes by compressing the material between two heated platens.
Transfer molding presses are used when intricate rubber parts are required. In this process, the rubber is preheated and then transferred into the mold cavity through a transfer pot. As a result, this method ensures even material distribution and high precision.
Injection molding presses are designed for faster production cycles and reduced material waste. These presses inject heated rubber directly into the mold cavity, making them ideal for high-volume production environments.
Multi-daylight presses feature multiple layers or “daylights,” allowing for the simultaneous production of several rubber parts. This configuration is particularly useful in large-scale manufacturing, where efficiency is key.
Applications of Vulcanizing Hydraulic Presses
These presses are utilized across various industries due to their versatility and reliability. For instance, the automotive industry relies on them for producing tires, seals, gaskets, and hoses, all requiring durability and precision.
In construction, vulcanizing presses manufacture rubber sheets, belts, and flooring materials, providing the strength and resilience needed in building applications. Moreover, the aerospace industry depends on these presses to create durable seals and gaskets that withstand extreme temperatures and pressures.
Furthermore, in the consumer goods sector, these presses produce everyday items like shoe soles, sports equipment, and household products, ensuring they are both durable and flexible.
Advantages of Vulcanizing Hydraulic Presses
One of the primary advantages of vulcanizing hydraulic presses is their ability to deliver precision and consistency. These machines offer precise control over pressure, temperature, and curing time, ensuring each product meets exact specifications.
Moreover, their high efficiency is another key benefit. Modern hydraulic presses feature automated systems that reduce manual intervention and increase production speed, which is critical in high-volume environments.
Additionally, the versatility of vulcanizing presses allows them to be used in the production of various rubber products, making them a valuable asset for different industries. Their durability is also notable, as these presses are built with robust materials designed to withstand continuous operation, ensuring a long service life with minimal maintenance.
Finally, their customizability allows manufacturers to produce a wide range of products with varying shapes, sizes, and complexities, making them ideal for businesses requiring flexibility in their production processes.
Maintenance and Troubleshooting
Regular maintenance is essential for ensuring the longevity and optimal performance of vulcanizing hydraulic presses. Therefore, it’s important to regularly inspect components like seals, hoses, and hydraulic fluids to prevent unexpected breakdowns and maintain efficiency.
Additionally, cleaning the press, especially around the mold area, is crucial to prevent contamination of the rubber and ensure product quality. Moreover, lubricating moving parts helps reduce friction and prevent wear, thereby extending the equipment’s lifespan.
Periodically calibrating the control system is also necessary to ensure accurate pressure and temperature settings, which is vital for maintaining consistent product quality.
However, common troubleshooting issues may include uneven pressure distribution, which can lead to inconsistent product quality. Worn seals or malfunctioning hydraulic cylinders may cause this issue. Furthermore, inconsistent heating could stem from faulty heating elements or poor heat distribution within the platens. Hydraulic leaks reduce pressure efficiency and should be addressed immediately by checking and replacing seals and hoses.
The Future of Vulcanizing Hydraulic Presses
Advancements in automation and materials technology continue to enhance the efficiency and reliability of vulcanizing hydraulic presses. Moreover, the integration of IoT (Internet of Things) technology allows for real-time monitoring and predictive maintenance, reducing downtime and increasing productivity.
Furthermore, the push toward sustainability is leading to the development of energy-efficient presses that minimize waste and reduce environmental impact. These innovations will ensure that vulcanizing hydraulic presses remain crucial in rubber manufacturing for years to come.
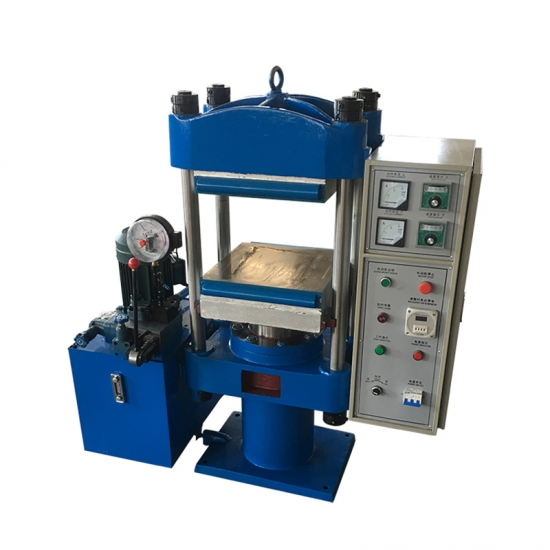
Welcome to Order
At Jiuying, we specialize in top-of-the-line vulcanizing hydraulic presses tailored to your specific business needs. Whether you’re in the automotive, aerospace, or consumer goods industry, our presses are designed to ensure consistent, high-quality production.
Moreover, our commitment to quality, innovation, and customer satisfaction makes us the ideal partner for your manufacturing needs. We offer customizable options to suit different production requirements and provide comprehensive after-sales support to keep your equipment running efficiently.
Therefore, we invite you to explore our product offerings to see how our vulcanizing hydraulic presses can enhance your production capabilities. Contact us today to discuss your specific needs and place an order. We look forward to helping you achieve your manufacturing goals.