The four-column hydraulic press, also known as an oil press, plays a crucial role in processing materials such as metals, plastics, rubber, wood, and powders. It operates by utilizing hydraulic oil pressure delivered by a pump, which is powered through an independent mechanism and electrical system. The press is controlled via a centralized button interface that offers three operational modes: adjustment, manual, and semi-automatic. However, like many hydraulic systems, pressure loss can occur, and this can negatively impact performance. Understanding the causes of pressure loss, as well as knowing how to troubleshoot and adjust the system, is essential for maintaining its efficiency and prolonging its lifespan.
Causes of Pressure Loss
Pressure loss in a four-column hydraulic press primarily results from friction and turbulence within the hydraulic oil flow. As the oil moves through the pipes, the friction between the oil and the internal surfaces of the pipes creates resistance. This resistance naturally increases as the length of the pipeline grows. Therefore, the longer the pipeline, the more friction it generates, which leads to greater pressure loss. Additionally, other components—such as elbows, joints, valve ports, and other fittings—introduce turbulence that disrupts the smooth flow of the oil, resulting in localized pressure losses throughout the system.
The total pressure loss is the cumulative effect of both frictional losses and localized losses. However, several measures can help minimize these losses. For instance, reducing the flow rate of the hydraulic oil can decrease friction and, consequently, lower pressure loss. Similarly, shortening the length of the hydraulic pipes and minimizing the number of bends and turns can significantly reduce resistance. Moreover, improving the smoothness of the pipe interior by selecting higher-quality materials or refining pipe finishes can further reduce friction, ultimately enhancing the efficiency of the system.
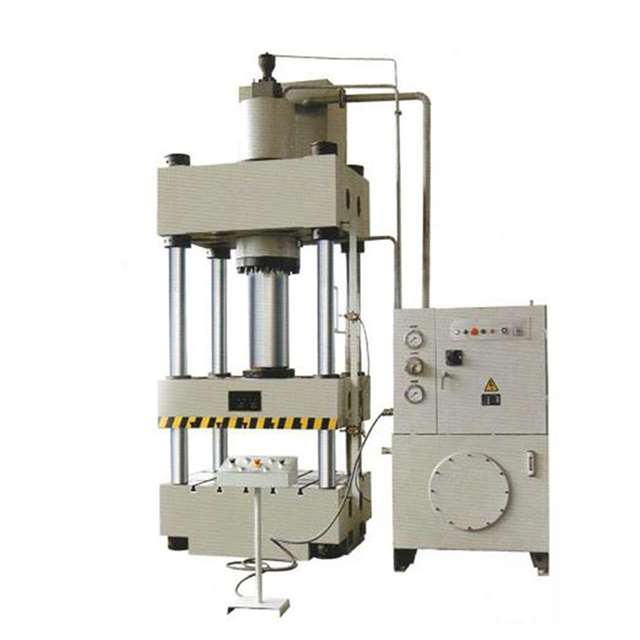
Adjusting and Debugging Pressure
Adjusting the pressure in a four-column hydraulic press is crucial for ensuring optimal performance. To maintain safe and efficient operation, the system pressure should always stay within the rated capacity of the pump and never exceed the nominal pressure, which represents the maximum pressure the system can safely handle. The working pressure of the press adjusts automatically based on the applied load. However, it is still important to set the system pressure to the maximum working pressure—also known as the nominal pressure—to ensure the system operates correctly without overloading.
To adjust the pressure, start by reducing the pressure on the relief valve and closing the pump outlet between the throttle valve and the reversing valve. After this, gradually increase the pressure by adjusting the valve to allow more hydraulic fluid into the system. During this process, it’s critical to monitor the pressure readings closely to ensure that it remains within the safe operational range, aligning with the nominal pressure. This careful approach ensures that the press operates safely and efficiently without exceeding pressure limits.
Pressure Calibration Procedure
Calibrating the pressure of the four-column hydraulic press requires precise steps to ensure the system operates within its designated pressure range. Begin by setting the action adjustment knob on the electric cabinet to the “adjustment” position. Then, press and hold the “two-hand operation” button to initiate the downward stroke of the press. The movement will be fast at first, but it will slow down once the fast-to-slow stroke switch engages. Once the upper and lower molds close, stop the downward motion and check the pressure gauge on the main cylinder to record the current pressure reading.
Afterward, press the “return” button to move the work surface upward. When the upward motion stops, adjust the pressure by rotating the pressure adjustment nut. Turning the nut clockwise will increase the pressure, while turning it counterclockwise will decrease it. Repeat this process until you achieve the desired pressure. By following this procedure, you can ensure that the system operates at the correct pressure, maximizing both functionality and performance.
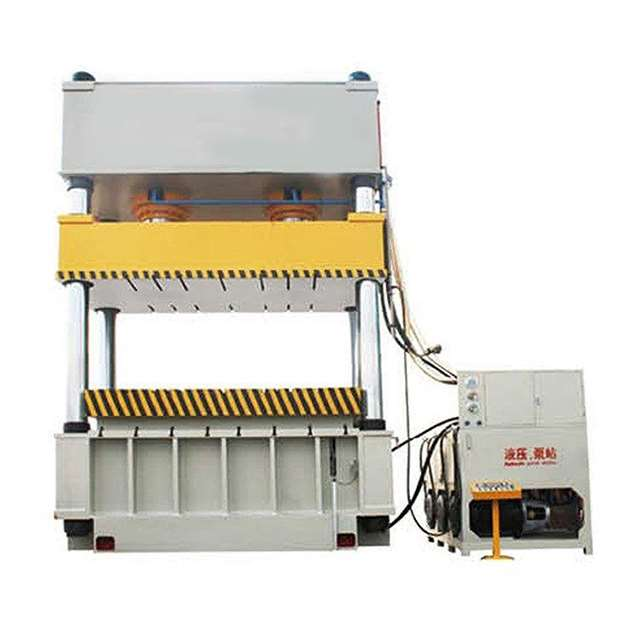
Why Choose Us
With over ten years of experience, Jiuying specializes in delivering high-quality hydraulic press solutions. We carry out rigorous testing and quality assurance processes to ensure that our equipment, including four-column hydraulic presses, functions reliably and efficiently over the long term. Furthermore, we offer tailored solutions designed to meet your specific operational needs, ensuring that you receive the best equipment for your application. In addition, all our products come with a one-year warranty, giving you peace of mind and protection for your investment.
Moreover, we provide 24-hour online support, so our expert team is always ready to assist you with any technical concerns or questions that may arise. We take pride in offering reliable, high-performance equipment backed by exceptional service, ensuring that your business can operate without interruptions. Choose us for all your hydraulic press needs and experience the difference in quality and support.
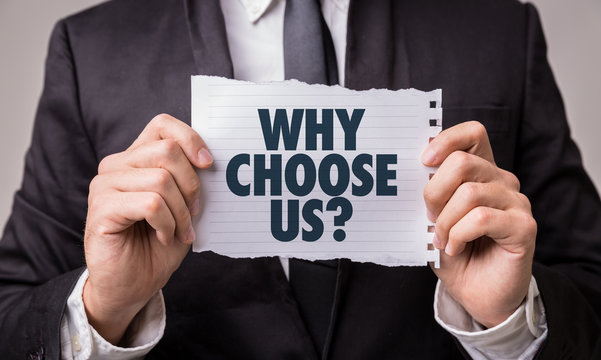