A kitchen sink is a vital item in every home, seamlessly combining functionality and design. As the centerpiece of the kitchen, it plays a key role in everyday tasks such as washing dishes, cooking, and cleaning. Given its importance, the production of kitchen sinks, especially stainless steel models, requires several precise and reliable processes. In this context, a hydraulic press machine becomes a vital piece of equipment in the production line. In this article, we will look at the role of hydraulic press machines in the production of kitchen sinks, describing their components, working principles, advantages, and applications.
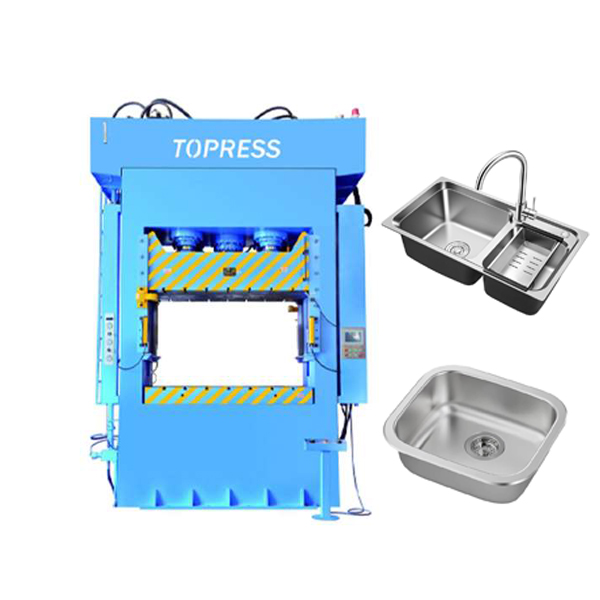
Hydraulic Press Components
A hydraulic press consists of several key components, each of which plays a critical role in its operation.
First, the hydraulic cylinder acts as the power unit of the machine, converting hydraulic energy into mechanical force. It contains a piston that moves up and down, driven by hydraulic fluid. In addition, a hydraulic pump creates the pressure needed to effectively move the piston.
In addition, control valves are required to control the flow and direction of hydraulic fluid, ensuring precision operations. These valves regulate the speed and force of the piston, allowing for detailed control over the pressing process. Meanwhile, the frame of the press supports all components and withstands the pressing forces, being made of high-strength steel to withstand significant pressure.
Finally, the die and punch are the tool components responsible for shaping the material. The die creates the negative shape of the part, while the punch applies force to form the material in the die. Together, these components are vital to the production of kitchen sink parts, as they determine the final shape and quality of the product.
The working principle of a hydraulic press
The hydraulic press operates on Pascal’s principle, which states that pressure applied to a closed fluid is distributed equally in all directions. This principle controls the hydraulic system, allowing it to generate significant force with a relatively low input pressure.
Here is a step-by-step description of how it works:
First, hydraulic fluid is injected into the cylinder. This specially formulated oil can withstand high pressures and temperatures. Then, a hydraulic pump increases the pressure of the fluid, often above 1,000 pounds per square inch. This high-pressure fluid is transferred to a piston inside the hydraulic cylinder, creating the force that moves the die and punch.
The material between the matrix and the punch is then formed by this force. High pressure provides a smooth course of the material into the matrix, forming an exact part. After the pressing, the pressure is reset, and the piston is returned to its original position, ready for the next cycle. This process is controlled by improved sensors and regulatory valves, which provides accuracy and repeatability .The Next Cycle. This Process Is Controlled by Advanced Sensors and Control Valves, Ensurging Accuracy and Repeataboly.
Advantages of using the hydraulic press in the production of kitchen sinks
Hydraulic presses have a number of key advantages in the production of kitchen sinks, which makes them a preferred choice for manufacturers.
Firstly, they provide high accuracy, guaranteeing a uniform and correct formation of components of the sinks. This accuracy is important for maintaining high standards of quality of kitchen sinks, since even minor deviations can lead to defects.
In addition, their versatility allows them to process various materials and complex forms, which makes them ideal for various stages of the production of sinks. Whether it is the formation of a deep sink bowl or cutting complex holes for drain and overflows, hydraulic presses are adapted to a number of tasks.
Moreover, their high efficiency accelerates the speed of production and output. Short cycles reduce production costs and increase throughput, helping manufacturers more efficiently satisfy the market needs.
Hydraulic presses are also distinguished by their economic efficiency. They have lower operating costs compared to mechanical presses, require less maintenance and have less moving parts. This reduces downtime and service costs.
Finally, improved management systems increase the security of the operator, making hydraulic presses with a reliable choice. Functions such as overload protection, emergency stop function and automated monitoring provide safe and efficient work.
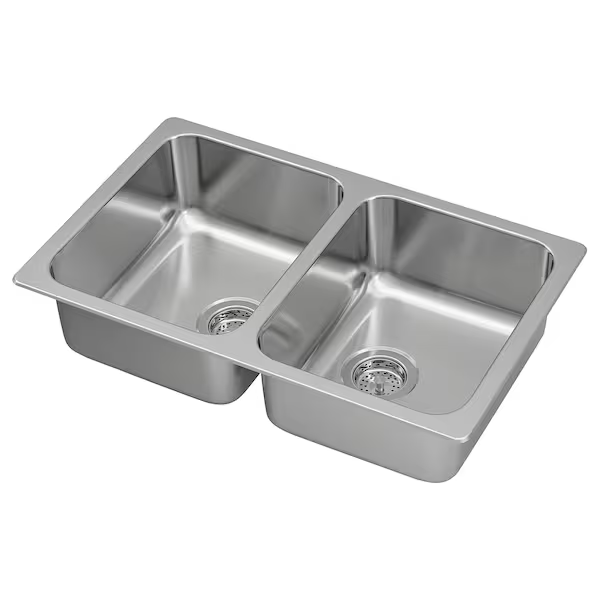
Use in the production of kitchen sinks
Hydraulic press machines are used at several stages of the production of kitchen sinks, each of which is crucial for achieving the quality and functionality of the final product. Here are some of the main applications:
1. Deep hood of the shell
A deep hood is a process in which a sheet metal blank is radically drawn into a molding matrix under the influence of a mechanical punch. This is the main application of hydraulic presses in the production of kitchen sinks. The machine uses uniform pressure to convert the flat sheet into a deep, seamless bowl of sinks without folds and defects. This process requires accurate control of the speed and strength of the press in order to avoid gaps or folds of the material.
2. Stamping and cutting
Hydraulic presses are used for stamping and cutting. Stamping involves molding or cutting the material by compressing it between the matrix and the punch. During the production of kitchen sinks, hydraulic presses stamp the drain holes, transfusive holes and other elements with high accuracy and repeatability. These operations are crucial to ensure the proper operation of the washing and compliance with its design characteristics.
3. Cutting and molding edges
After the initial molding, pruning and the shape of the edges of the sink are crucial for compliance with design and safety standards. Hydraulic presses effectively cope with these tasks, providing clean, exact edges that increase the overall quality of the sink. This step is important for both aesthetics and functionality, since gross or uneven edges can cause problems during installation and use.
4. Polishing and surface finishing
Hydraulic presses also help at the stages of polishing and surface decoration. Using specialized stamps and tools, these machines can help achieve a smooth, polished surface, which increases the aesthetic attractiveness and functionality of the sink. Politing eliminates any surface defects and gives the sink of high -quality finishes, which is simultaneously attractive and easy to clean.
Welcome to the site where you can order a hydraulic press
Hydraulic press machines play an important role in the modern production of kitchen sinks, offering unsurpassed accuracy, effectiveness and versatility. They play an important role in deep hood, stamping and decoration, guaranteeing that each kitchen sink meets the highest quality standards.
To improve your production line, consider our advanced hydraulic presses. We have developed our high -quality presses to meet the needs of the industry and provide optimal results. Contact us today to discuss your needs. Let us help us transform your production process using our innovative solutions. We are looking forward to partnership with you and supporting your success in the production of kitchen sinks.