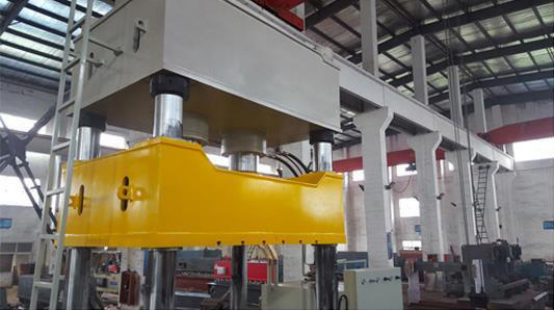
When the piston rod of the hydraulic cylinder is extended or retracted under the action of oil pressure, uneven speed often occurs, sometimes accompanied by vibration and abnormal noise, which causes vibration of the entire hydraulic system and drives other components of the main engine to vibrate. It often occurs during the host debugging process, and sometimes the speed is faster, and this phenomenon will be alleviated. In addition to this phenomenon caused by the hydraulic system piping, the vibration generated by the hydraulic cylinder itself often causes this phenomenon.
Causes of the crawling phenomenon of hydraulic cylinder
Low-speed crawling is caused by gas in the rod chamber and rodless chamber of the hydraulic cylinder
Because the gas is mixed in the hydraulic oil, under the action of pressure, the volume changes, and even the gas explodes instantaneously under the action of high pressure, which causes the speed of the hydraulic cylinder to be unstable.
Low-speed crawling caused by improper design clearance of hydraulic cylinder
The sliding fit gap between the piston and the cylinder body, the piston rod, and the guide sleeve inside the hydraulic cylinder is too large, causing uneven pressure on the sliding surface, causing uneven friction, and causing the hydraulic cylinder to crawl at low speed; if the sliding fit gap is too small, In addition, there are tolerances in the manufacture of parts, which will also cause uneven pressure on the sliding surface, resulting in uneven friction and low-speed crawling of the hydraulic cylinder.
Low-speed crawling caused by uneven friction of guide elements in the hydraulic cylinder
The guide materials and non-metallic support rings commonly used in hydraulic cylinders, especially the non-metallic support rings are not uniform in size, and some non-metallic support rings increase or decrease in size with the change of oil temperature, that is, the poor dimensional stability in the oil directly causes the fit clearance It is easy to cause the speed of the hydraulic cylinder to be unstable.
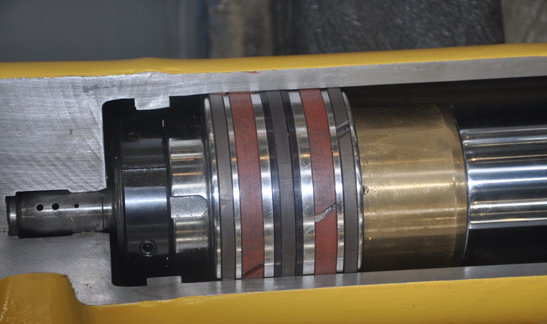
Low-speed crawling of hydraulic cylinders caused by seal material problems
Commonly used sealing materials for hydraulic cylinders include nitrile rubber, polyurethane rubber, polytetrafluoroethylene, etc. Due to the hardness, strength, and followability of the material, it directly affects the friction between it and the sliding surface. In addition, for lip seals, oil pressure fluctuations The contact pressure between the sealing area and the contact surface changes, which causes the change in the hydraulic cylinder speed.
Influence of machining accuracy of parts
The processing accuracy of the inner wall of the hydraulic cylinder and the surface of the piston rod has a great influence on the low-speed stability of the hydraulic cylinder. In particular, geometric accuracy has a greater impact, in which straightness is the key, and it is the most difficult to ensure straightness during processing. For hydraulic cylinders with long strokes, the straightness of the inner wall of the hydraulic cylinder and the surface of the piston rod is the main factors affecting the low-speed stability of hydraulic cylinders.
Solutions
Low-speed crawling caused by gas in the rod chamber and rodless chamber of the hydraulic cylinder
The purpose of the exhaust can be achieved by repeatedly operating the hydraulic cylinder. If necessary, an exhaust device is installed in the pipeline or the two chambers of the hydraulic cylinder to exhaust when the hydraulic system is working.
Low-speed crawling caused by improper design clearance of hydraulic cylinder
The sliding fit clearance between the piston and the cylinder block, the piston rod, and the guide sleeve inside the hydraulic cylinder can be correctly designed.
Low-speed crawling caused by uneven friction of guide elements in the hydraulic cylinder
It is recommended to use metal as the guide support first, such as QT500-7, ZQAL9-4, etc. If a non-metallic support ring is used, it is recommended to use a non-metallic support ring with good dimensional stability in the oil, especially since the thermal expansion coefficient should be small. The thickness of the support ring must strictly control the dimensional tolerance and the uniformity of the thickness.
For low-speed crawling of hydraulic cylinders caused by seal material problems
It is recommended to use polytetrafluoroethylene as the seal combination seal ring when the working conditions permit, such as the commonly used gray ring, step seal, etc.; if the lip seal is selected, the recommended material is butyl rubber or similar Material seals have better followability.
Other methods
In addition to the above methods, if allowed, the safety factor of the cylinder wall thickness of the hydraulic cylinder should be selected as large as possible to increase the thickness of the cylinder, especially for cylinders used under high-pressure conditions, so as to reduce oil pressure. The cylinder block is deformed, and the deformed cylinder block will also cause the hydraulic cylinder to crawl at a low speed.
Regular maintenance of the hydraulic press
The phenomenon of hydraulic crawling is one of the common faults of hydraulic presses, so regular maintenance of hydraulic presses is also very important. If you are interested in the complete process, please read my blog–How Do We Maintain The Hydraulic Press?
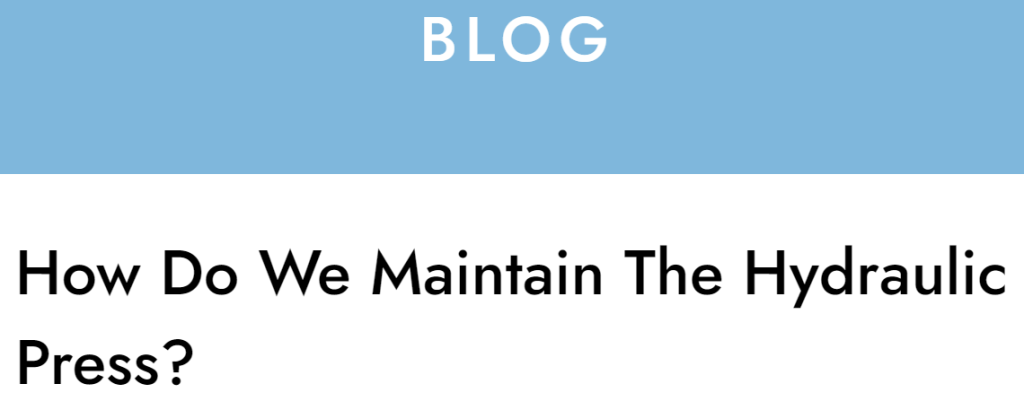
To eliminate such faults, it is necessary to check that the pressure control valve and flow control valve is blocked by dirt in the oil, and if the problem is found, it should be eliminated in time.
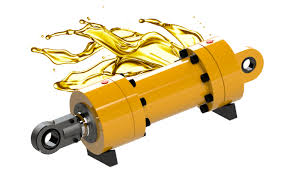
Also, check the condition of the hydraulic oil to see if the hydraulic oil is seriously polluted; whether there is water entering the oil; check whether the viscosity of the oil meets the requirements; whether the hydraulic oil is emulsified, etc. When the above phenomenon occurs, the hydraulic oil should be replaced in time.