The four-column hydraulic press is widely recognized for its reliability and precision in industries that require high-quality pressing and forming. However, like any complex machine, it can occasionally encounter faults that disrupt normal operations. Hydraulic press repair is essential to maintain optimal performance and prevent costly downtime. Recognizing these issues early on and addressing them effectively can significantly improve efficiency, minimize downtime, and extend the life of your equipment. Below, we explore the most common faults and provide practical repair solutions to ensure your press continues to perform at its best. Regular hydraulic press repair is key to keeping your equipment running smoothly for years to come.
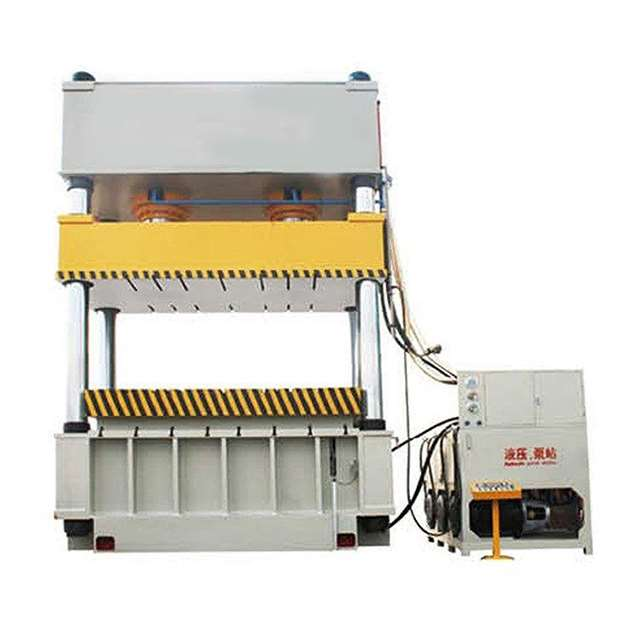
Hydraulic System Failures
One of the most frequent issues with four-column hydraulic presses is hydraulic system failure. When this occurs, the machine may experience unstable or insufficient pressure, leading to slower working speeds and difficulty generating the required pressing force. This problem is often caused by low hydraulic oil levels, worn seals, or damaged hydraulic components.
To resolve this, the first step is to check the hydraulic oil level. If the oil is low, adding more oil—ensuring it’s the right type as specified by the manufacturer—can often solve the problem. Additionally, it’s essential to inspect the seals for any signs of wear or damage. If seals are compromised, replacing them will restore the system’s integrity. Furthermore, regular inspections for leaks and maintaining adequate fluid levels are key preventive measures that can help avoid these problems in the future.
Electrical Control Failures
Electrical control issues are another common challenge faced by four-column hydraulic presses. These problems can manifest in various ways, such as the motor failing to start or solenoid valves not functioning properly. In most cases, electrical failures are due to poor wiring connections, malfunctioning electrical components, or issues within the control system.
To troubleshoot electrical control failures, start by inspecting the wiring. Check for loose or improperly connected wires. If you find any, tighten or reconnect them as needed. Afterward, check the electrical components, including relays, switches, and fuses. Worn or damaged components should be replaced immediately. By performing regular electrical inspections, you can catch potential issues before they lead to significant malfunctions, ensuring a more reliable and efficient operation of the hydraulic press.
Mechanical Failures
Mechanical failures are also relatively common in four-column hydraulic presses. These failures can present themselves in the form of unusual noises, sluggish movement, or decreased efficiency. Mechanical problems often arise from insufficient lubrication or wear and tear on components like bearings, gears, or shafts.
To address mechanical issues, start by checking the lubrication levels. If the lubricant is dirty or insufficient, replace it with fresh oil to ensure smooth operation. Next, inspect mechanical components for signs of wear. If any parts—such as bearings or gears—appear damaged, replacing them promptly is essential to prevent further damage. Regular lubrication, along with timely replacement of worn parts, is critical to reducing mechanical failure and prolonging the machine’s service life.
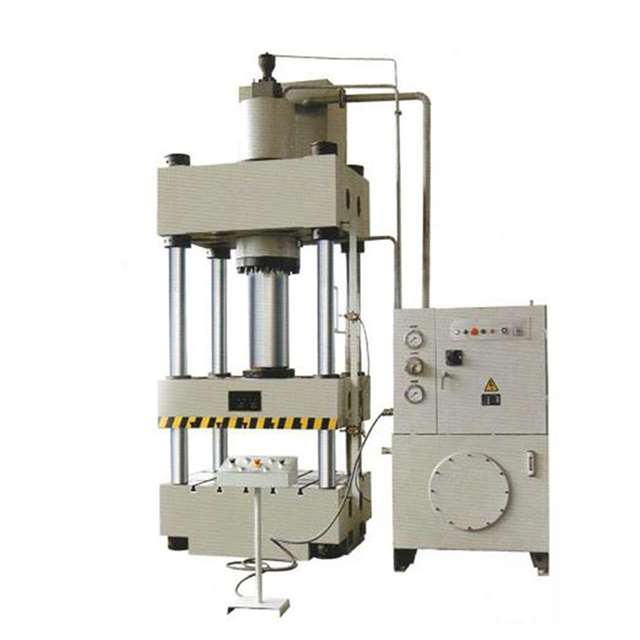
Preventive Maintenance and Inspection
Preventive maintenance plays a crucial role in avoiding many of the common faults associated with four-column hydraulic presses. By regularly inspecting and servicing the machine, you can identify potential problems before they escalate into costly repairs or unplanned downtime.
For the hydraulic system, routine checks of the oil levels and periodic oil changes are essential. Additionally, regularly inspect seals, hoses, and fittings for any leaks or signs of deterioration. By replacing worn hydraulic components promptly, you can maintain proper pressure and improve the system’s overall efficiency.
In terms of the electrical system, make sure to inspect all wiring connections and test components like switches, relays, and solenoids. Routine electrical inspections can help prevent unexpected breakdowns and ensure that the press operates reliably.
For the mechanical system, it’s crucial to monitor lubrication levels and check for signs of wear on moving parts. If you notice unusual noises or sluggish movements, address these immediately to avoid further damage. Regular hydraulic press repair, including lubrication and timely replacement of worn-out components, will ensure your press runs smoothly and efficiently.
Why Choose Us?
With over ten years of experience in the industry, we offer customized solutions for all your hydraulic press needs. We have a proven track record of successful partnerships with clients worldwide, reflecting the reliability and high performance of our machines. Our hydraulic presses come with a one-year warranty, and we provide 24-hour online support to assist you whenever you need it. Contact us today to learn more about how we can help you maintain your four-column hydraulic press in optimal condition!
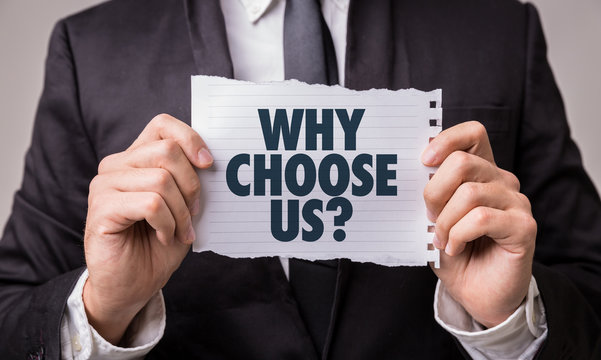