The 2000-ton four-column hydraulic press plays an essential role in producing graphite crucibles. These crucibles are vital for smelting alloy tool steels and non-ferrous metal alloys. Made from a blend of graphite, clay, silica, and wax stone, they offer excellent thermal conductivity, high-temperature resistance, and outstanding chemical stability. During production, operators place trimmed graphite material into a mold. The press then applies high pressure to compress and form the crucible. Thanks to its robust three-beam, four-column structure, the press ensures uniform texture and high efficiency. The press produces one crucible in just 3–5 minutes. Each mold can last for 4–6 cycles, making the press indispensable in graphite crucible production.
Key Features of the 2000-Ton Hydraulic Press
The hydraulic press features an independent hydraulic system. This system includes a pump, motor, valve manifold, oil tank, and cooling device. Together, these components work seamlessly to ensure smooth operation. The electrical control system provides flexibility by supporting both inching and semi-automatic modes. Operators can adjust pressure and stroke settings to meet specific production needs. The system also incorporates a pressure-maintenance function to ensure consistent operation throughout the process.
For safety, the press includes several critical features. These include an emergency stop button, thermal protectors, circuit breakers, and anti-slip devices. The electric contact pressure gauge continuously monitors the upper chamber pressure of the main cylinder. Once the system reaches the set pressure, it automatically halts the press. This prevents overpressure and ensures safety. Additionally, the press’s integral cast steel structure guarantees long-term durability. It resists deformation and rust, even with prolonged use.
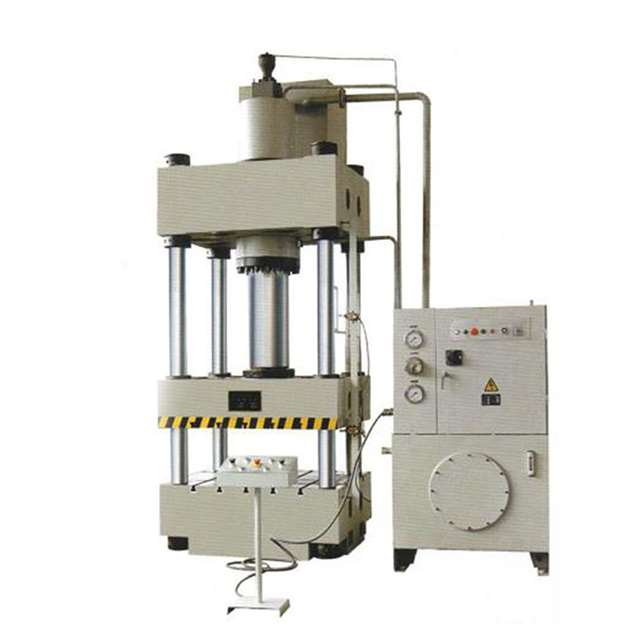
Advantages of the 2000-Ton Hydraulic Press
The 2000-ton hydraulic press is designed to operate in high-temperature environments. It excels in metal smelting and casting applications. The press can withstand the intense impact and pressure of molten metals. This ensures stable and efficient operation under challenging conditions. With its large capacity and high efficiency, the press can process substantial amounts of material at once. This reduces both production time and cost. In fact, the press produces one crucible every 3–5 minutes. This significantly boosts productivity.
The press is equipped with advanced control systems. These systems provide precise control over pressure, speed, and position. As a result, the press ensures consistent product quality. Furthermore, the press is versatile. It can handle crucibles of varying sizes, shapes, and weights. Mold replacement is simple and quick, making it adaptable to different casting processes. The hydraulic system is more energy-efficient than traditional mechanical equipment. This reduces energy consumption and helps meet environmental standards.
Safety remains a top priority. The press includes several safety features, such as temperature monitors, hydraulic protection devices, and emergency stop buttons. These features ensure both operator safety and equipment reliability. The press undergoes rigorous testing to guarantee long-term performance, stability, and durability.
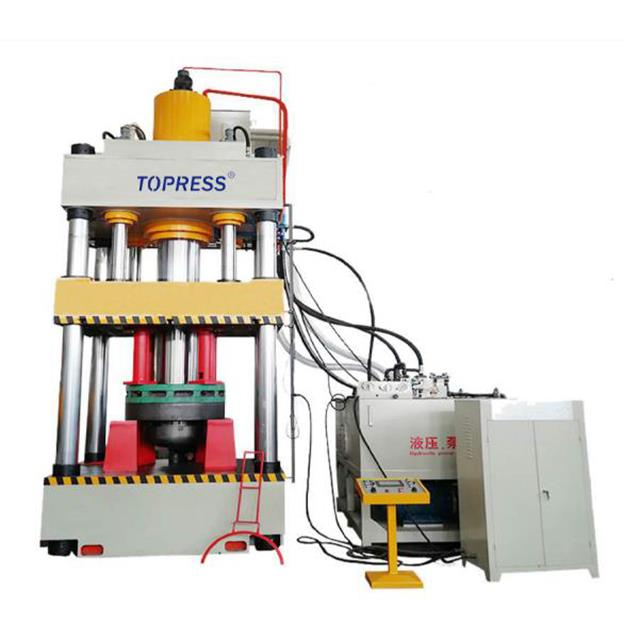
Why Choose Us?
With over 10 years of experience in hydraulic press manufacturing, Jiuying specializes in delivering high-quality, customized solutions. We focus on meeting our customers’ specific needs. Our team is committed to designing, testing, and manufacturing products that meet the highest standards for performance, reliability, and efficiency. We also provide comprehensive after-sales support. This includes a one-year warranty and 24-hour online service to ensure peace of mind and long-term satisfaction.
If you are interested in learning more about our 2000-ton four-column hydraulic press or any other products, please contact us. We are here to provide reliable, cost-effective solutions tailored to your production needs.
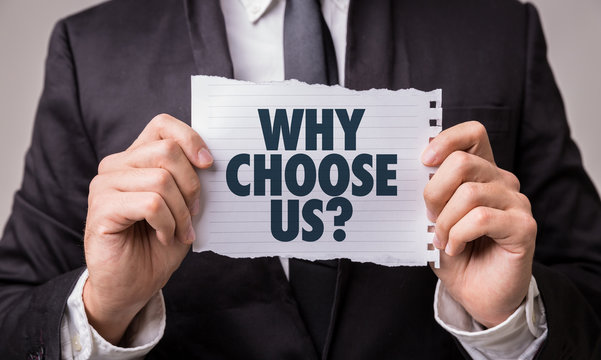